by DOYLE McMANUS
Get rid of the sweatshops, not the jobs that millions need
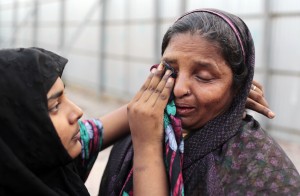
One year ago this week, the eight-story Rana Plaza garment factory collapsed in Bangladesh’s capital city of Dhaka, killing 1,129 people. The building’s top floors had been added illegally, and their weight caused the lower stories to buckle. Many of the victims were young women who had been sewing low-priced clothes for Western brands, earning a minimum wage of about $9 a week. It was the worst disaster in garment industry history.
In the year since Rana Plaza, inspectors commissioned by U.S. and European clothing companies have scoured Dhaka, checking factories that supply brands to Western retailers. What they found was alarming: More shoddy high rises in danger of collapse. Exits blocked with chains and steel bars. Exposed electrical wiring and other fire hazards. Stairwells without steel fire doors.
“The way the system is set up, this is going to keep happening,” said Jason Motlagh, a freelance journalist who investigated the problem on a grant from the Pulitzer Center on Crisis Reporting.
With wage levels about one-fourth of China’s, Bangladesh has become one of the world’s biggest suppliers of mass-market garments. And producing garments cheaply has been possible in part because government and local factory owners don’t enforce basic safety regulations.
“They actually have really good safety laws on the books,” Sajeda Amin, a Bangladeshi sociologist, said last week. “The problem is, the people who are in charge of implementing them can be paid off.”
Facing the likelihood of more disasters, a few American companies have pulled out of Bangladesh; others have cut their production, restricting it to a few modern facilities. But most have stayed, betting that they can keep production going while holding manufacturing facilities to basic safety standards that the government has neglected.
“Our test is: Can we prevent another Rana Plaza?” said Ellen O. Tauscher, a former California congresswoman who heads one of two industry groups working on safety in Bangladesh. “We’ll never prevent all factory fires. But can we prevent building collapses and factory fires that result in people dying?”
The mostly European group has publicly released the results of 10 factory inspections. The American-led group hasn’t released any results, saying it’s waiting for approval from the government of Bangladesh first.
Officials in the two groups say they’re trying to cooperate with each other, but they’ve also been quick to trade accusations. “We’re trying to do something for workers in Bangladesh, and we walked straight into a political campaign,” Ms. Tauscher complained.
So what’s a well-meaning consumer to do?
Bangladeshis, including labor activists, don’t want anyone to boycott clothes made in their country. In one of the world’s poorest nations, sweatshops are paradoxically one of the bright spots in the economy.
“For many of the women in these factories, this kind of work was the better option,” Ms. Amin said. “The best thing would be to expand their opportunities instead of boycotting.” Already, she noted, political pressure since Rana Plaza has forced the government to increase the garment industry minimum wage to about $16 a week.
Most consumers, I suspect, don’t want to buy clothes made in unsafe factories. But knowing which clothes were manufactured responsibly isn’t easy at this point. For labor conditions in Bangladesh to improve, consumers and retailers will need to remember the Rana Plaza disaster not just on its first anniversary but for years after that.
Doyle McManus is a columnist for the Los Angeles Times.