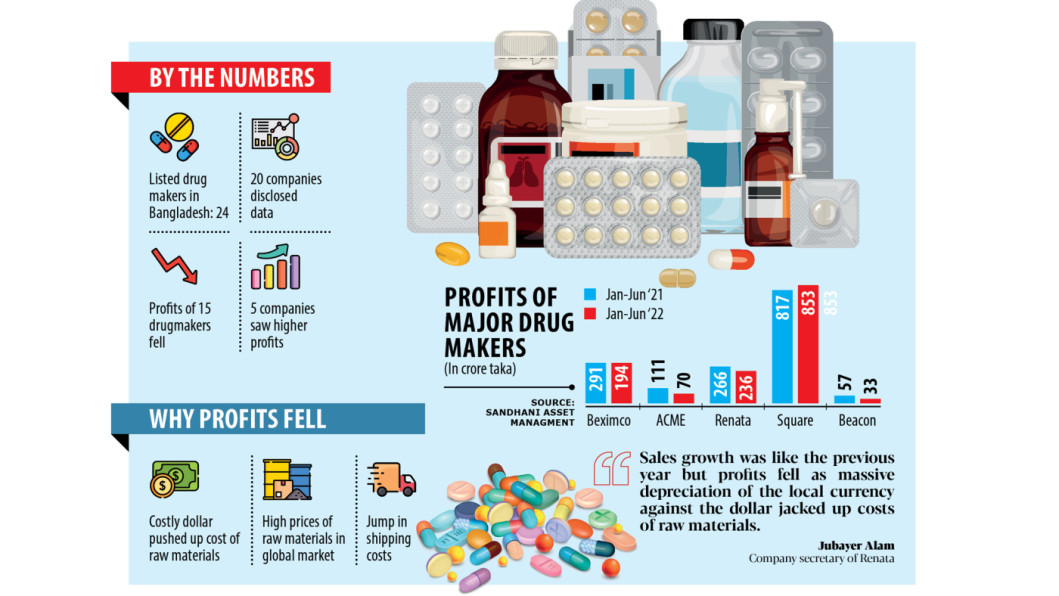
Most of the drug makers in Bangladesh posted lower profits in the January to June period of 2022 owing to the higher cost of raw materials driven by a continuous fall of the local currency against the US dollar.
Twenty-four pharmaceutical companies listed in the stock markets publish their financial reports regularly. Of them, 20 have disclosed their data for the last financial year of 2021-22 that ended on June 30.
The data, compiled by Sandhani Asset Management Company, showed that profits dropped for 15 pharmaceutical companies in the six-month period, while it rose for five companies.
“One of the main reasons for the profit decline was higher raw material costs and a sharp depreciation of the local currency against the US dollar,” said Mohammad Asad Ullah, company secretary of Beximco Pharmaceuticals.
Higher freight charges also pushed up the cost of production.
Owing to the supply disruptions and pent-up demand, the cost of shipping a container on the world’s transoceanic trade routes increased seven-fold in the 18 months following March 2020, while the cost of shipping bulk commodities spiked even more, according to an analysis of the International Monetary Fund in March this year.
One of the leading drug makers in Bangladesh, Beximco Pharmaceuticals logged 33 per cent lower year-on-year profits of Tk 194 crore between January and June.
Similarly, ACI, Reckitt Benckiser Bangladesh, Beacon Pharmaceuticals, Active Fine Chemicals, Central Pharmaceuticals, AFC Agro Biotech, Advent Pharmaceuticals, Silva Pharmaceuticals, Silco Pharmaceuticals, and Acme Pharmaceuticals posted lower profits during the identical half.
Jubayer Alam, company secretary of Renata, said sales volume grew almost at the same pace as in the previous year in January-June but profits slid for the depreciation of the taka and the escalated costs of raw materials.
The national currency lost its value by 10 per cent against the American greenback, hitting Tk 93.45 on the last day of June this year on the interbank exchange market against Tk 84.90 on the same day a year earlier as the taka began falling amid the fast depletion of the reserves.
This piled up pressure on the medicine manufacturers since the country relies on the global markets for most of the Tk 1,000-crore ingredients needed to produce drugs.
“The profits of the pharmaceuticals industry shrank significantly in recent times as raw material costs rose 20 to 25 per cent on average,” said M Mohibuz Zaman, chief operating officer of ACI Pharmaceuticals.
But drug makers have not increased the prices of medicines proportionately to the rise in the cost of production, so profits fell, said Jubayer Alam.
“The companies have adjusted the prices in many cases recently, so the impact on the profit would be lower in the coming days.”
Renata’s profits dropped 11 per cent year-on-year to Tk 236 crore in the second half of 2021-22.
Square Pharmaceuticals, the largest drug maker in Bangladesh, posted a 4.4 per cent higher profit at Tk 853 crore.
“Our product basket is much bigger than most of the other companies and we are not heavily dependent on a few products,” said Muhammad Zahangir Alam, chief financial officer of Square Pharmaceuticals.
“So, our profits were not impacted. Operational excellence has also influenced the performance.”
The pharmaceuticals sector, which meets 97 per cent of the local demand, witnessed a 12.1 per cent compound annual growth over the last five years. The market size was Tk 27,500 crore as of June 2021, according to an analysis of UCB Asset Management.
Pharmaceuticals exports stood at $83 million in the January-June period, almost unchanged from the same period a year earlier, data from the Export Promotion Bureau showed.
Foreign sales, however, rose finally, fetching $188 million in 2021-22, up more than 11 per cent from $169 million a year earlier.
And analysts hope that exports from Bangladesh may cross $1 billion within the next two to three years as the door to the US market, the world’s largest, has opened for some drug makers because of their high level of compliance.
If local manufacturers can tap the opportunities in the US market, the value may cross even $5 billion within the next five to six years, they say.